Destructive testing of materials
With destructive testing, in contrast to non-destructive testing, no consideration has to be given to the further use of the components. There are no limits, which allows for a much more versatile assessment of the material. This plays an essential role especially in the context of damage assessment. Here, the full spectrum of destructive material testing is usually called upon. This includes, on the one hand, the recording of material parameters such as tensile strength, elongation at break, impact energy or hardness, and on the other hand, the metallographic evaluation of sections under the light microscope and scanning electron microscopy (SEM analysis). Corrosion examinations, in which a component is destroyed at least superficially, are also included.
The goal in damage assessment (also called damage analysis) is to clarify the causes in order to avoid further failures. This often requires interdisciplinary work between destructive and non-destructive testing, but also a comprehensive wealth of experience on the part of the inspectors and engineers.
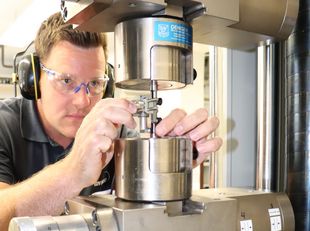
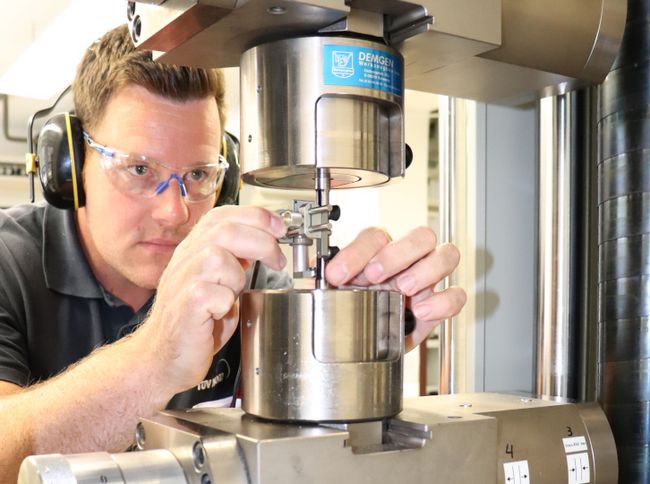
TÜV NORD’s services within the scope of destructive materials testing
Due to their training and experience, our engineers and technicians are able to process your enquiries in a solution-oriented and efficient manner. Our further training programmes ensure that we always have up-to-date materials expertise. Our solutions are characterized by an interdisciplinary approach. Based on comprehensive engineering diversity in diverse fields of work, TÜV NORD offers comprehensive services from a single source. Based on a comprehensive library and the latest regulations, we provide you with reliable and sustainable results. Furthermore, our company is recognized worldwide as a "Third Party Organisation".
Certified testing laboratories
- accredited according to DIN EN ISO/IEC 17025
- certified according to ISO 9001
TÜV NORD's testing laboratories support you in solving problems in the operation of your plant or in the manufacture of your products. We offer you comprehensive material tests completely from one source.
Another focus is the examination of components that are used in the creep rupture area or are subject to thermal effects. We carry out these tests for you directly on site in the plant. They are carried out in a quasi-nondestructive manner, so that the condition of the plant is not changed.
Destructive test methods in our test laboratories
Bending tests
Bending tests on various materials and destructive weld tests are carried out in three- and four-point bending tests, depending on the specifications. With regard to formability testing, sheets or tubes are analyzed at room temperature in the as-delivered condition or after annealing in the folding test.
Pressure and burst tests
For strength tests of pressure vessels, pressure equipment, fittings or other pressure-bearing components, a bursting pit is available at the Institute for Destructive Material Testing, in which high-pressure tests can be carried out until the failure of an object. High-pressure pumps are available for hydraulic pressures up to 4,000 bar and gas pressures up to 600 bar.
Furthermore, pressure threshold tests up to 450 bar are possible. Accompanying measured variables, such as volume increase and deformation, can be used to record the onset of plasticization and the extent of progressive permanent deformation.
Service life examinations / component metallography
In order to be able to evaluate the condition of plant components in the area of creep stress, the Institute for Materials Testing carries out metallographic examinations (using the replica technique), mobile hardness tests (according to the Vickers and UCI methods - see item Hardness Testing), geometric measurements (wall thickness and ovality measurements) and surface tests (PT or MT - see item Non-destructive Testing) on site in the plants using VGB Guideline R 509 L. The evaluation of the microstructure imprints is carried out using the VGB standard S 517.
In the case of fire damage, we use these examination methods to characterize the thermal influence on the material. For the characterization of microstructures, we have created an internal evaluation standard for steel materials to assess thermal influence/damage.
Fatigue strength / component tests
The fatigue strength is the load limit that a dynamically loaded component can permanently withstand without any noticeable signs of fatigue or failure. In order to be able to make statements about the dynamic load capacity of a component, a specified number of load cycles can be applied to a specimen in the fatigue test. With the Zwick/Roell Amsler 500 HFP 5100 high-frequency pulsator it is possible in a short time to vibrationally test reinforcing steel and similar bar-shaped and dynamically loaded components in the tensile range up to a maximum test load of 500 kN, thus simulating the loads "in the life" of a component under laboratory conditions.
Corrosion tests
In our corrosion laboratory, we investigate the resistance of metallic materials and their general corrosion behavior in aggressive media. The results obtained provide valuable information when assessing corrosion damage or evaluating corrosion systems.
In addition, we offer standard test methods for determining the resistance of stainless steels to intergranular corrosion, e.g. in accordance with DIN EN ISO 3651-2 or SEP 1877 or ASTM A262, test method E. The so-called Huey test in accordance with DIN EN ISO 3651-1 or ASTM A262, test method C for determining the resistance of stainless steels to localized corrosion in strongly oxidizing acids is also included, as is testing of pitting and crevice corrosion resistance in accordance with ASTM G48.
Do you have questions about materials testing? We are at your disposal!
Please feel free to contact our locations directly.
Certification body for NDT personnel
TÜV NORD operates a certification body for non-destructive testing personnel (NDT personnel), which is accredited according to ISO/IEC 17024. Our certification body offers the possibility of having your company's NDT personnel certified according to DIN EN ISO 9712.
For personnel performing non-destructive testing on permanent connections of pressure equipment, the certification is considered an endorsement according to the European Pressure Equipment Directive 2014/68/EU. Our qualification tests, which are prerequisites for certification, are performed in both fixed and mobile testing centers.
Not what you are looking for?
Learn more about our non-destructive testing services or start at our materials testing home page.