Logistik – Das sollten Sie wissen
Dies und das von A nach B bringen? Intelligente Logistik von heute muss mehr leisten, viel mehr. Die globalen Regularien sind kompliziert, der Material- und Warenfluss ist komplex, die Konkurrenz ist gnadenlos. Intelligente und digitalisierte Prozesse sind zentrale Elemente der Logistik der Zukunft und können Unternehmen unter anderem auch dabei unterstützen, für eine nachhaltigere Logistik zu sorgen. Mit unserem Know-how maximieren Sie die Effizienz und nutzen die Chancen: denn wer die Regeln kennt und die Tools präzise einzusetzen weiß, der sitzt sicher im Sattel.
Logistik gehört heute und in Zukunft zu den Wachstumsbranchen des Wirtschaftsstandortes Deutschland – doch mit dem steigenden Warenverkehrsaufkommen wird auch der Qualifizierungsbedarf für alle Mitarbeiter innerhalb der Logistikkette immer anspruchsvoller und vielseitiger. Wir helfen Ihnen, das jeweils aktuelle Vorschriftenwerk richtig einzuordnen und die sich daraus ergebenden Schritte in Ihre Arbeitsabläufe einzuleiten.
Digitalisierung in der Logistik
Auch in Logistikunternehmen geht die Digitalisierung zügig voran. Logistik 4.0 ist das Schlüsselwort, um den Ansprüchen der Industrie, wie Vernetzung, Dezentralisierung, Echtzeitfähigkeit oder Serviceorientierung gerecht zu werden. Doch wo fängt man an, neue, innovative Techniken zu integrieren und Arbeitsprozesse zu optimieren? Starten Sie erfolgreich in die Logistik der Zukunft, nehmen Sie Ihre Mitarbeiterinnen und Mitarbeiter mit und identifizieren Sie die richtigen Prozesse, um aktuelle Logistik Trends in die Praxis umzusetzen.
Artikel von A - Z
- Ladungssicherung und Verantwortung
- Logistik 4.0
- Nachhaltigkeit und Logistik 4.0
- Patent auf KI anmelden
Unsere Empfehlungen für Sie
Haben Sie Fragen?
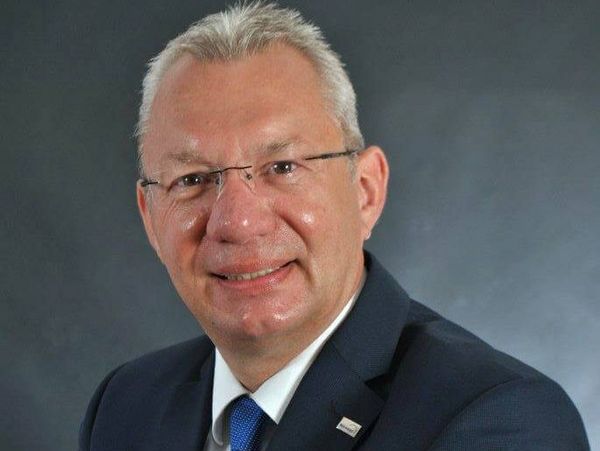
Produktmanager Logistik
Am TÜV 1, 30519 Hannover
Tel.: +49 511 998-62273
Fax: +49 511 998-62075
pflucks@tuev-nord.de