Hydrogen storage: From compressed gas storage to hydrid storage
Various methods are available for the storage of hydrogen (H2). Compressed storage and cryogenic liquid storage of hydrogen are the most commonly used in industry. Compressed hydrogen storage can take place in steel containers or containers made of a composite material. They are used, for example, for truck transport, vehicles and hydrogen storage in industry or at hydrogen filling stations. The pressure level here is between 20 and 90 bar. To store hydrogen in vehicles, the automotive industry relies on the use of pressure tanks, where the pressure level is up to 70 bar. This means that fuel cell vehicles have a similar range to petrol cars. In addition, it is generally possible to store hydrogen under extremely low overpressure (0.0022 bar) in gasometers.
Storage in salt caverns is suitable for extremely large quantities of hydrogen. These have a geometric volume of 70,000 to 600,000 m³. Pore storage, which is also underground, also offers great potential as a hydrogen storage facility. Metal hydrids (chemical compounds of metals with hydrogen), on the other hand, are used to store smaller quantities of hydrogen. Other processes, including the storage of hydrogen in complex hydrids or the physisorption of hydrogen in porous materials, are currently still being researched or are only used in niche areas.
Hydrogen is a topic with many facets - from production, transport and storage to use. With our expertise, know-how and many years of experience, we are an independent partner for safety and security by being able to test, inspect and certify various aspects of hydrogen technology.
Compressed gas storage of hydrogen
Natural gas storage is closely linked to the future of hydrogen storage, as corresponding storage facilities for natural gas can also be used for hydrogen. Hydrogen is stored under high pressure in specific containers and under extreme cooling in liquefied gas storage facilities. Underground compressed gas storage of hydrogen also offers great potential. Background on natural gas supply: Germany has only small natural gas reserves and has to import 80 % of its demand. Against the background of a reliable energy supply, gas storage facilities therefore play an important role. Huge, mostly underground facilities can compensate for seasonal fluctuations in demand as well as supply bottlenecks. Almost a third of Germany's annual natural gas consumption is available as a reserve in this way. In addition, aboveground storage facilities are used to manage consumption peaks at the local level or to cover industrial demand.
Above-ground hydrogen storage: stationary and mobile pressure vessels
Small- to medium-volume gas tanks in metal construction are used for above-ground compressed gas storage. Tubular storage tanks embedded in the ground allow high nominal pressures and the storage of larger gas volumes. Specific high-pressure tanks are used for the storage of hydrogen. For storage, hydrogen is compressed under high pressure due to its physical properties, in some applications up to 1,000 bar. Liquid hydrogen (LH2) requires a storage temperature of -253 °C, for which larger containers with efficient insulation are needed.
Gaseous hydrogen compressed under high pressure (CGH2= compressed hydrogen) is stored and transported in cylindrical containers made of steel, whereas lighter, carbon-fibre-coated containers made of aluminium or plastic are used as hydrogen storage in fuel cell vehicles. In addition, hydrogen can be stored for small applications in metal hydrid storage tanks or on a large scale in liquid carrier media (LOHC = liquid organic hydrogen carrier).
Underground compressed gas storage of hydrogen
In the area of geological possibilities for compressed gas storage, both the cavities of salt domes (caverns) and more difficult-to-access "pore spaces" of former gas and oil deposits, as well as water-bearing aquifers, can be used for hydrogen storage. However, it should be noted that only part of the storage volume of an underground storage facility can be utilized.
A certain minimum pressure must be maintained in the reservoir to preserve the mechanical properties of the reservoir rock as well as for optimal operation during the injection and withdrawal of the gas. The portion of the gas that is needed to maintain this "minimum operating pressure" and thus cannot effectively be used is called "cushion gas". The proportion of gas that can be stored and withdrawn at any time is called "working gas". The relative proportion of cushion gas to working gas can vary greatly depending on the type of storage.
Hydrogen storage in caverns
In the course of the development and expansion of the hydrogen economy, underground hydrogen storage facilities can make an important contribution to the stable supply of renewable energies. Cavern storage facilities located in salt dome cavities are already proven storage facilities for natural gas, for example. They are also part of an infrastructure that still needs to grow significantly in order to store hydrogen on a relevant scale and make it usable according to demand. The first research caverns for hydrogen are currently being used to establish model regions in which green hydrogen can be produced, stored and distributed with the help of power-to-gas technologies.
Hydrogen storage using caverns also allows rapid access to the stored supplies, with an average cavern of 60 m in diameter and 300 m high achieving a working gas volume of 100 million standard cubic metres. In the case of hydrogen, this would correspond to an energy quantity of 300 GWh at a filling pressure of 175 bar. In view of these figures, the conversion of existing cavern storage facilities and the construction of new ones can promote the use of hydrogen on a large scale. In this context, hydrogen storage in salt caverns must meet the same requirements as storage in natural gas caverns:
- Sufficient capacity to compensate for seasonal and diurnal fluctuations in demand
- Ability to cover peak loads (peak shaving)
- Economic efficiency of storage operation.
In Great Britain and the USA, salt caverns have been used for hydrogen storage for quite some time. In Germany, the first hydrogen research caverns are currently being built as promising real laboratories of a sector-coupled energy infrastructure.
Pore storage for the storage of hydrogen
Empty oil or natural gas reservoirs or even water-conducting aquifers consist of rock layers that have natural cavities and the appropriate permeability. They are also naturally sealed to the surface. These pore reservoirs can hold large quantities of gas, which, however, can only be stored at high pressure and only slowly released again, as it has to flow through the porous rock again and again.
Pore storage facilities are particularly suitable for balancing seasonal fluctuations in demand. The capacity of pore storage facilities is not surpassed by any other storage facility: Western Europe's largest natural gas storage facility in Rehden, Lower Saxony, extends over three depleted natural gas deposits at a depth of 2 km and offers a working gas capacity of 4 billion cubic metres over an area of 8 km². Thus, the potential of pore storage is also enormous for hydrogen storage.
Solid hydrogen storage: metal hydride storage
With regard to mobile and portable applications, the storage of gaseous hydrogen in metal hydride storage tanks is worth considering. So far, the compact solid fuel storage tanks still have a relatively low storage capacity for hydrogen compared to their own weight. However, their low storage pressure offers advantages for the safe storage of hydrogen. In this respect, these hydrogen storage systems differ in particular from current high-pressure or cryogenic storage technologies. As part of an established hydrogen infrastructure, advanced metal hydrid storage systems can be increasingly used in the future - for example as fuel cell system components in vehicles or in fuel cell-powered small devices such as portable computers.
Hydrogen filling stations and refuelling stations
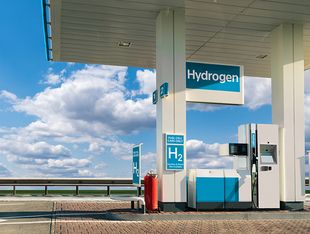
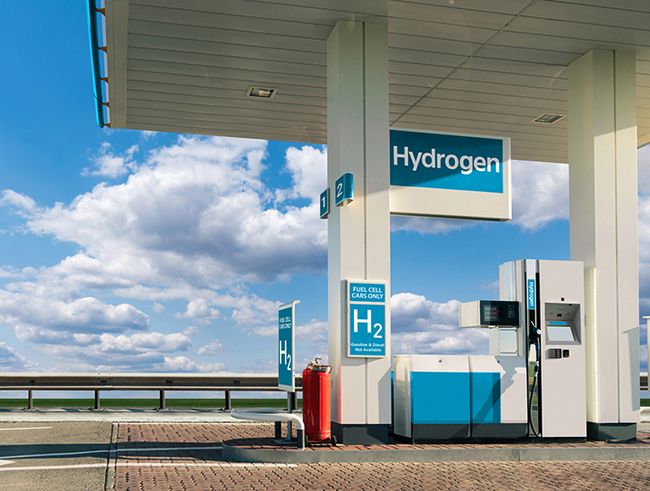
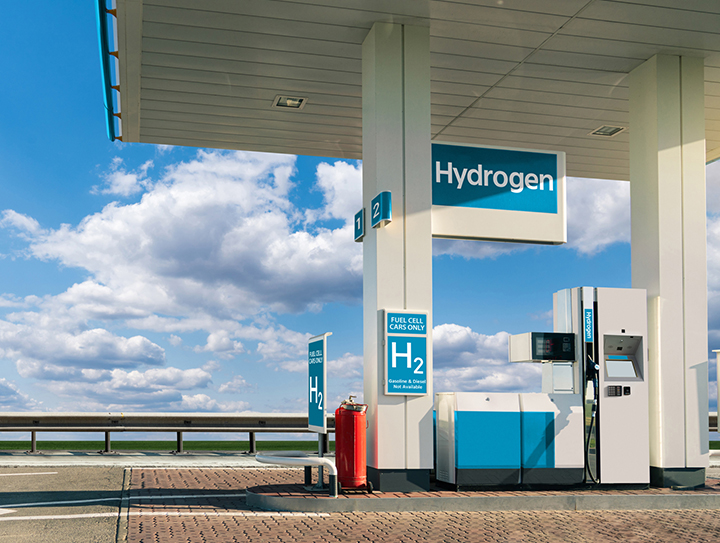
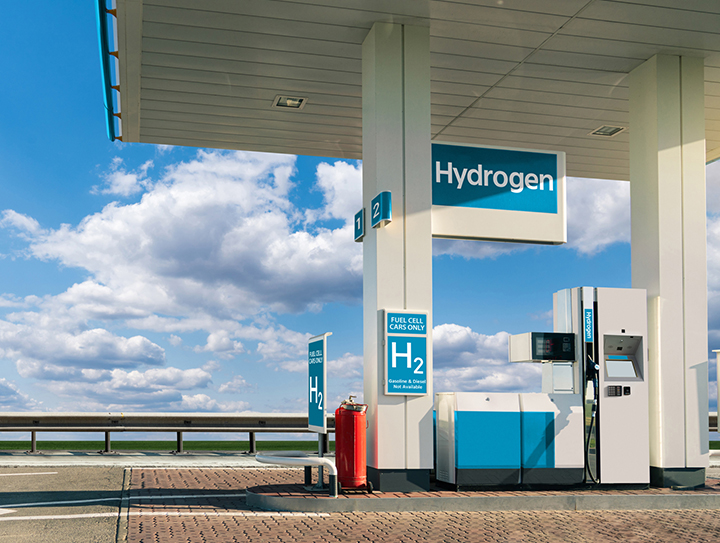
Hydrogen refuelling of road and rail vehicles takes place via refuelling stations that enable supply at different pressure levels. In addition to stationary H2 filling stations, there are also mobile refuelling stations for hydrogen cars. The hydrogen storage and compression technology is of importance and is chosen depending on the initial state of the hydrogen (liquid or gaseous) and the number and type of vehicles to be refuelled. The high pressure levels also pose a special challenge to the sealing technology of tank systems.
As part of the development of a hydrogen infrastructure, a network of stationary hydrogen filling stations is being built in Germany that will facilitate the refuelling of road vehicles with gaseous hydrogen. In addition, there are small plants, for example for the refuelling of fuel cell forklifts, mobile hydrogen filling stations for specific local demand coverage, and refuelling stations for fuel cell-powered trains. Most refuelling stations are supplied with hydrogen from hydrogen trailers, some have an elektrolyzer in which hydrogen is produced on site.
Filling up with gaseous hydrogen at the H2 filling station
Gaseous hydrogen is stored in refuelling stations at H2 filling stations in pressure vessel bundles, elevated tanks or underground cylindrical steel tanks. For refuelling, compressors reduce the volume of the hydrogen and compress it to the required pressure levels. Currently, most hydrogen filling stations are designed to fill cars with 700 bar within about three minutes. Refuelling stations with appropriately large compressors can also supply commercial vehicles with 700 bar.
In order to refuel hydrogen buses and hydrogen trucks, refuelling stations require a 350 bar tap point, while the pressure tanks of trains are filled at 250 bar. Thermal management also plays an important role in the process flow of a refuelling station. Hydrogen is brought to a temperature of -40 °C for gaseous refuelling. For storage in the gaseous state, this is done by refrigeration equipment; for storage in the liquid state, a cryogenic pump is used to heat the -253 °C cold hydrogen.
Liquid hydrogen at hydrogen filling stations
While the storage and transport of liquid hydrogen has long been common practice, its use as an energy carrier in vehicles is still being researched. After initial trials with liquid hydrogen-powered passenger cars, trucks are now the main focus of vehicle development and the adaptation of refuelling stations. Here, refuelling procedures are being tested that avoid the boil-off effect of gaseous refuelling and also make the complex data communication between H2 filling station and vehicle superfluous. Boil-off refers to the continuous evaporation that occurs when heat enters tanks containing liquid hydrogen.
Compared to gaseous hydrogen, liquid hydrogen is much colder (temperature: -253 °C) and requires significantly improved insulation of pressure vessels and pipelines. On the other hand, due to its higher energy density, it also allows refuelling at a lower pressure level and the use of smaller and lighter tanks with a greater vehicle range. After building the first pilot stations for refuelling with liquid hydrogen and a successful test phase, liquid hydrogen technology could make an additional contribution to the decarbonization of road transport, especially in the area of long-distance transport.