SCC Certificate: Focus on occupational safety
On trading estates and in large factories, external contractors are regularly used for technical services or work contracts. The employees from these contractors are not so familiar with the work processes and other circumstances at the different sites and so cannot always recognise possible sources of hazard and danger. This results in risks, which can in turn lead to disturbances in the workflow and in the worst case even to considerable injury or damage to people, material assets or the environment.
Certification according to the SCC Standard is directed towards companies who work as contractors in large factories and on industrial estates. However, it is suitable for all manufacturers and service providers, both in Germany and abroad.
TÜV NORD offers you, as a contractor, certification according to the SCC Standard (Safety Certificate Contractors) so that you can demonstrate compliance with the most important occupational safety requirements. The certificate demonstrates to your customers that you fulfil the fundamental standards regarding occupational safety and health and the environment (HSE). In many sectors, both at home and abroad, the certificate is an essential prerequisite in order to gain access to tender processes.
Why is SCC certification useful? Your benefits
- Optimisation of management processes and more efficient working
- Avoidance of illness and accidents among your employees
- Avoidance of damage to the environment and physical assets
- Avoidance of work delays or interruptions for yourself and for your clients, therefore less financial burden on your company
- Greater safety awareness on the part of your employees
- Your workers and managers will benefit from increased qualifications with regard to occupational safety, health and environmental protection.
- You fulfil customer requirements, become more competitive on the (international) stage, and gain an entrance ticket to the market.
- You are assured a high level of legal compliance and can provide suitable proof through demonstrable fulfilment of relevant requirements.
There are three versions of SCC certification
The size of your company and the services you offer determine which of the three versions is right for you:
SCC* is a certification with a limited number of aspects for companies with up to 35 employees who do not make use of subcontractors themselves for supply of technical services.
The main emphasis of this form of certification is on assessment of the HSE management activities directly at the workplace. The assessment includes an on-site visit with assessment of the level of occupational safety in place at the site where your employees are contracted.
Prerequisites for SCC* certification
- Use of the safety, health and environmental (HSE) management system for at least three months.
- The 27 mandatory questions in the SCC* checklist are answered correctly
- Determination of the accident rate according to SCC and keeping to, or falling below, the limit for the certification.
- Standardised training of your personnel and management personnel with HSE test successfully completed.
SCC** is unlimited certification for companies with more than 35 employees and for companies with fewer than 35 employees who make use of subcontractors for technical services.
Alongside assessment of the HSE management activities directly at the workplace, the main emphasis of this form of certification is on implementation of these activities in your own company (headquarters). The assessment includes an on-site visit with assessment of the level of occupational safety in place at the site where your employees are contracted.
Prerequisities for SCC**certification
- Use of the safety, health and environmental (HSE) management system for at least three months.
- The 40 mandatory questions and at least five of the nine possible supplementary questions in the SCC** checklist are answered correctly.
- Determination of the accident rate according to SCC and keeping to, or falling below, the limit for the certification.
- Standardised training of your personnel and management with HSE test successfully completed.
SCCP is unlimited certification for companies with more than 35 employees and for companies with less than 35 employees who make use of subcontractors for technical services, and who also have to fulfil special requirements of the petrochemical industry or from refineries.
Alongside assessment of the HSE management activities directly at the workplace the main emphasis of this form of certification is on implementation of these activities in your own company (headquarters). The assessment includes an on-site visit with assessment of the level of occupational safety in place at the site where your employees are contracted.
Prerequisites for SCCP certification
- Use of the safety, health and environmental (HSE) management system for at least three months.
- The 44 mandatory questions and at least three of the five possible supplementary questions in the SCCP checklist are answered correctly.
- Determination of the accident rate according to SCC and keeping to, or falling below, the limit for the certification.
- Standardised training of your personnel and management personnel with HSE test successfully completed.
The SCC checklist
The SCC checklist contains all criteria that are significant for the assessment during the audit and for the subsequent certification decision. Detailed information on the SCC Standards can be found on the website of the German Accreditation Body, DAkkS (Deutsche Akkreditierungsstelle).
FAQs
Depending on the version which is chosen, the SCC checklist contains a defined number of relevant questions. The objectives, the minimum requirements to be fulfilled and the necessary documents, and also the personnel to be interviewed/observed during the on-site audit are assigned to each question. The questions are divided into 12 topics:
Chapter 1: HSE: Policy, organisation and commitment of the management
Chapter 2: HSE hazard assessment
Chapter 3: HSE training, information and instruction
Chapter 4: HSE awareness
Chapter 5: HSE project plan
Chapter 6: Environmental protection
Chapter 7: Preparation for emergency situations
Chapter 8: HSE inspections
Chapter 9: Occupational physician services
Chapter 10: Procurement and inspection of machines, devices, equipment and work materials
Chapter 11: Procurement of services
Chapter 12: Report, record and investigation of accidents, near accidents and insecure situations
The number of accidents should be reduced over the long term. This is why the SCC Standard puts a special focus on accident statistics according to UH (SCC). For initial certification, an accident rate of UH (SCC) of 40 may not be exceeded. For recertification, the value must have been reduced by 20 per cent.
Certification according to SCC Standard involves a two-stage assessment: firstly through review of documents, and secondly through a visit to the company site. The on-site inspection and the document review ensure that your HSE management system fulfils the requirements of the standard.
Of course you would like to know what budget you need to set aside for SCC certification. In order to be able to tell you exactly, we will need a few details from you. These are influencing factors such as your average number of employees and projects, and which version of SCC you have chosen.
Please get in touch with us – we will be pleased to write you an offer free of charge.
In the course of the certification procedure a representative number of your projects – in other words activities at the site of your customers – will be visited. The projects selected for the audit (construction sites, workshops, production areas) should be representative types of projects for your company. The aim is to be able to observe and interview as many employees as possible while at work.
According to the SCC standard, your active employees (workers and managers) have to demonstrate that they have passed an HSE test. In order to ensure a consistent standard of training, test content and criteria are specified in the SHE test questionnaire. Active employees are those who are directly involved in the provision of the service.
SCC certification can be performed individually, but can also be combined with other certification procedures such as ISO 9001, ISO 14001, ISO 45001 and ISO 50001. Why not speak to us about the possibilities and the benefits? We will be pleased to give you further information.
Certification with TÜV NORD
TÜV NORD is recognised as a well-established and reliable provider of inspection and certification services, assessing fulfilment of legal regulations and voluntary standards all over the world. We only employ experienced specialists – and our auditors, who come from many sectors of industry, are trained to a very high level and use standardised methods. This means we can guarantee independence, neutrality and continuity in all our services to you.
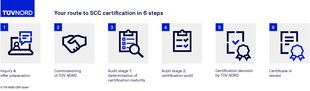
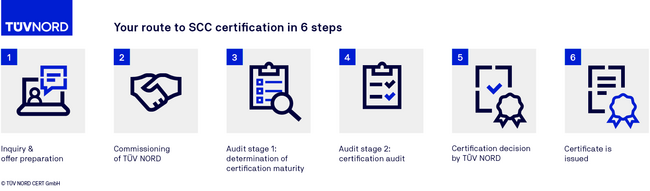

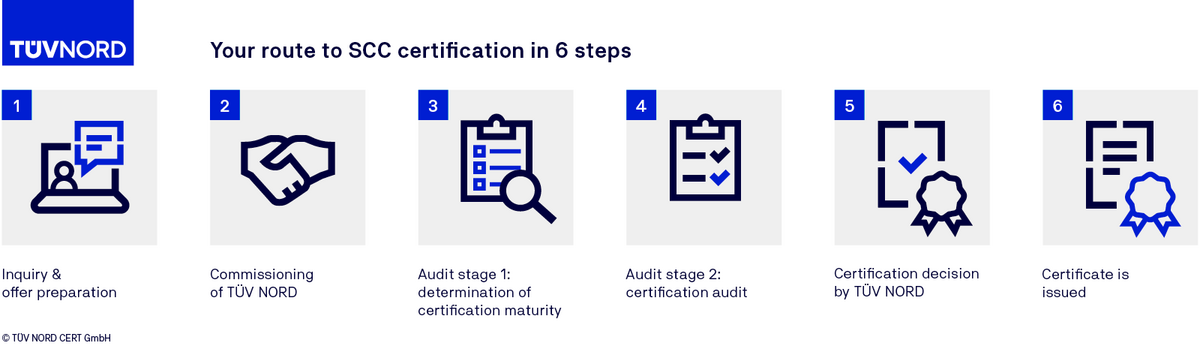